OUR SERVICES
We provide a full range of project services from process development and initial feasibility studies to final start-up, operations, and maintenance including the following services:
- Project management, estimating, cost control and planning
- Technical and economic feasibility studies
- Bench and pilot scale test work
- Process engineering and development
- Basic and detailed engineering and design
- Procurement
- Construction management
- Plant start-up commissioning and training
- General consultancy
- Due diligence
We have the capability to organize and manage projects of all sizes from inception through execution to production. Services are tailored to the specific requirements of individual projects and customers and range from minor consulting as
Feasibility Studies and Technical Evaluation
In the area of international phosphate feasibility studies and technical evaluations, our record over the past thirty years is unparalleled. During this period, feasibility studies and in-depth evaluations have been completed for such as Al Jalamid and Umm Wu'al (Saudi Arabia), Sra Ouertane (Tunisia), and Bayovar (Peru).
LABORATORY AND PILOT PLANT CAPABILITIES
We’re the only company that has its own phosphates lab with pilot plants for both phosphate beneficiation and phosphoric acid.
Because of this, we understand the test work better than anyone else. Our lab is located at our Florida, USA, office, where we can help develop your best possible flow sheet, design plants for specific feedstocks and provide the appropriate process guarantees.
We are the only company that can offer complete solutions without involving third-party technology suppliers, creating seamless project execution for our customers.
The facilities are comprised of an analytical laboratory, a bench-scale metallurgical ore testing laboratory, and a fully equipped beneficiation pilot plant capable of either batch or continuous operation which allows JT to design the optimum flowsheet. In addition, the Lakeland facility has a pilot-scale phosphoric acid pilot plant equipped to produce concentrated phosphoric acid (MGA and SPA) as well as specialized equipment to produce and test phosphate fertilizers such as monoammonium phosphate (MAP), diammonium phosphate (DAP), single super phosphate (SSP), triple super phosphate (TSP), and nitrogen-phosphate-potassium (NPK) fertilizers.
Our laboratory facilities are used to supplement feasibility studies, develop process design data, and perform contract research for customers such as the Florida Institute of Phosphate Research.
To support beneficiation and fertilizer testing programs and to provide timely data for tests in progress, we maintain a full “phosphate capable” analytical laboratory adjacent to the pilot plants.
We are a member of the Association of Fertilizer and Phosphate Chemists and take part in the sample check program to ensure the highest level of accuracy in our test results.
Our analytical capabilities are:
- Typical rock analyses performed include: P2O5, acid insoluble residue (A.I.), CaO, MgO, Fe2O3, Al2O3.
- Additional analysis – Trace Metals includes: As, Cd, Co, Cr, Cu, Mn, Mo, Ni, Pb, Se, Sr, Ti, U, V, and Zn
- Rock concentrates analysis typically includes: P2O5 , acid insoluble residue (A.I.), CaO, MgO, Fe2O3, and Al2O3, as well as Na2O, K2O, F, W.S. Cl, Total Cl, SO3, CO2, LOI, total SiO2, acid insoluble SiO2, acid soluble SiO2, organic C, H2O, and Cd.
- Phosphoric acid and fertilizer analytical capabilities include the above as well as: water soluble P2O5, citrate soluble P2O5, citrate insoluble P2O5, available P2O5, Free Acid, acid emf, hardness and percent nitrogen.
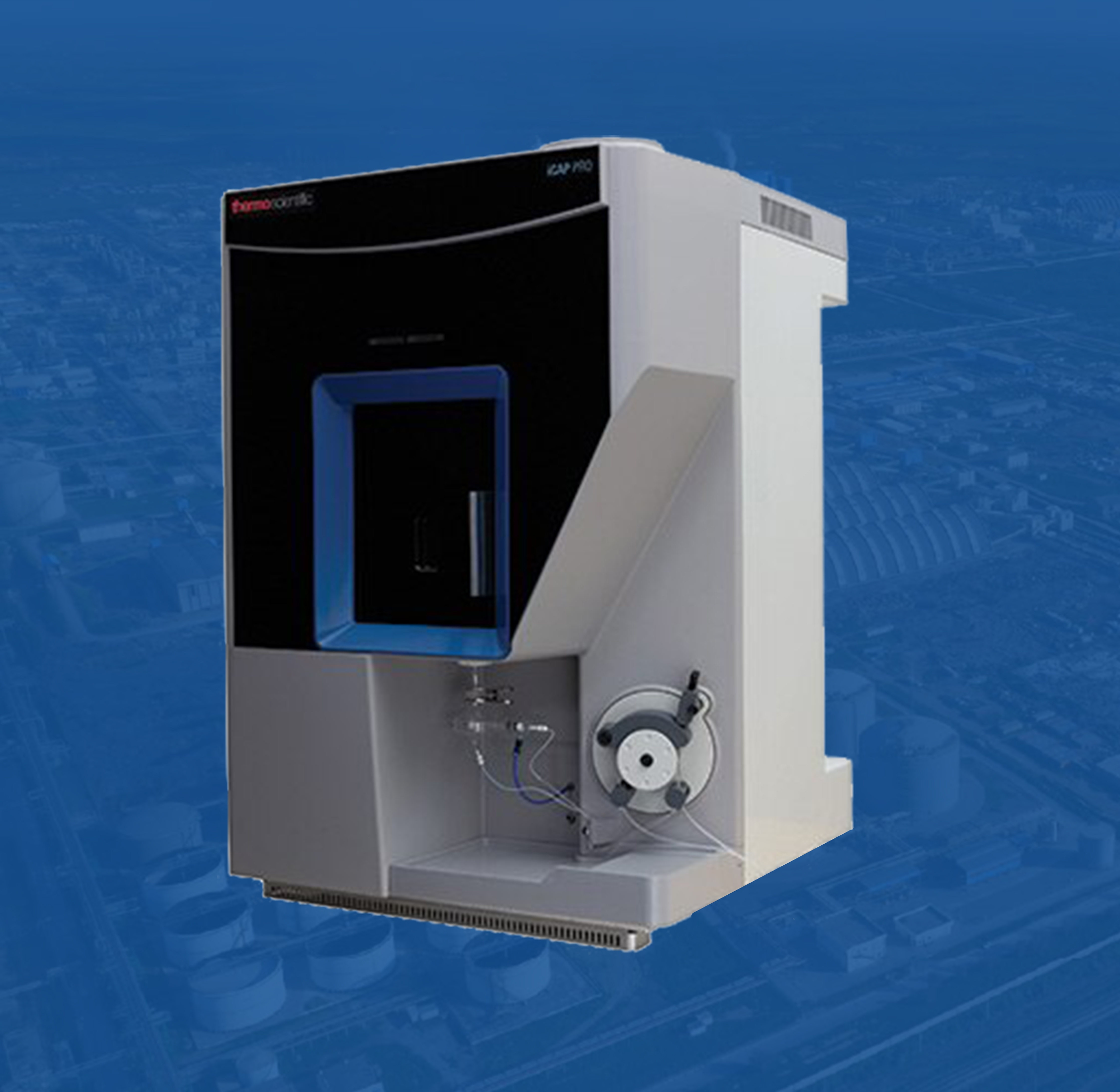
Laboratory Analysis & Bench Scale Tests
Our metallurgical laboratory provides testing for ore enrichment, process development, flowsheet layout and plant design as well as assessment studies for existing operations. The facilities include crushing, grinding, magnetic separation, size classification, scrubbing, gravity separation, flotation, and dewatering. Our laboratory offers in-plant sampling campaigns and diagnostic services.
BENEFICIATION PILOT TESTS
Beneficiation pilot plant testing is a critical step necessary to build and operate a robust plant. The pilot plant is modularized to accommodate various configurations to suit the requirements of any given ore processing flowsheet. The unit operations can include any of the following: rod ball milling, classification (screens, hyrdocyclones, hydrosizers) flotation, and dewatering.
Our pilot plant throughput rates can vary depending on the flowsheet, customer requirements, equipment requirements, availability and size and consistency of the ore. The throughput capacity of our pilot plant for recent programs has ranged from 300 kg/h to 1000 kg/h.
The ability to integrate beneficiation with phosphoric acid processing allows for optimization of both operations.
PHOSPHORIC ACID PILOT TESTS
The phosphoric acid pilot plant is used to evaluate the suitability of phosphate rock for the commercial production of phosphoric acid and granular fertilizers. The pilot plant results provide the expected product quality and the sizing criteria for phosphoric acid plant design. These results also allow us to determine process guarantee values for production, quality, recovery, and raw material consumptions.
The phosphoric acid pilot plant operates at a range of 600 to 3200 g/h of dry rock and can be configured to operate in dihydrate (DH), hemihydrate (HH), or hemi-dihydrate (HDH) modes.
The tests can be run for different rates and reactor sizes depending on the availability of rock samples and the objective of the tests.
We provide pilot plant assessment by comparing the pilot data with its proprietary database of other commercial phosphate rocks. The tests provide a correlation between product acid strength and filtration rates and establish an optimum sulfate level. Other tests often performed in conjunction with phosphoric acid pilot plant testing include gypsum particle size distribution, granulation testing, reactivity testing and corrosion testing.
Results from the pilot plant have been used to successfully design very large full-scale plants with scale down factors more than 500,000:1.
FERTILIZER PILOT TESTS
The product acid can also be used to produce granular fertilizers such as TSP, SSP, MAP, DAP and NPK fertilizers. The fertilizer may then be analyzed for nutrient levels, moisture, pH, and hardness. Our pilot plant produces small samples of MAP, DAP, NPK, TSP and SSP to evaluate the physical and chemical properties of these fertilizer products. MAP, DAP and NPK are produced in granular forms, while TSP and SSP can be produced in powder or granular form.
Due Diligence
Through the operating and engineering experience accrued by our personnel, we have developed special skills in the preparation of due diligence, feasibility evaluations and the formulation of critical financial, commercial, and engineering opinions for the phosphate industry.
OPERATOR TRAINING
We offer operator training programs and plant familiarization programs both on site and virtual for the training/orientation of the owner’s plant operating personnel. These programs are customized for each client for specific needs.
Front-End Engineering and Detailed Design
We provide full-service engineering specializing in the front-end engineering and detailed design of both mineral processing and chemical plants for the phosphate industry.
COMMISSIONING AND STARTUP
We provide start-up, process, instrument and mechanical engineers at the site during construction, pre-commissioning, start-up, initial operation, and performance test runs. The presence of these engineers is intended to assist, advise, and finally train the owners personnel in plant operation. We have demonstrated experience, when participating throughout the project life, of bringing the plants up to full process capabilities very shortly after start-up.
PROCESS PERFORMANCE
We are committed to meeting customer goals by providing high quality and customized plants. Therefore, each project is treated uniquely. During the project life for a new plant or new operation in a brownfield plant, our laboratory can do testing to determine Process Guarantees. Process Guarantees ensures customer expectations for a design can be met. Given the varied ore bodies around the world, this is an important point. We also apply sound design principles for plant integrity and reliability. This point is often overlooked or simply sacrificed for CAPEX, but our designs can result in unparalleled plant operating factors and run times between required turnarounds.